THE OUTPUT DRIVETRAIN SECTION
The output section of the SMR Mega Torq 727 receives extensive performance upgrades to assure the
transfer of the torque without failure.
The 5 pinion front planetary (R1)has been manufactured with a steel spline to prevent
the spline stripping common with aluminum carriers. and considerable friction reduction is acheived by replacing the thrust
washers with large enclosed Torrington needle bearings(R2). The governor assembly(R6)
has been eliminated and the park gear (R7)lightened for weight reduction. Our
billet steel output support (R8)utilized a large roller bearing providing the greatest axial support and the
strongest assembly available. We Utlize the 16 element, 6 bolt, low roller clutch(R9) which
is absolutely the strongest on the market. Both annulus units (R3&R5)receive extensive
reinforcement for reliability. The low/reverse drum(R10) is supported by a large internal roller
bearing, reducing drag, and integrated with the billet support.
These components transmit the torque through a polished output shaft
which is supported by a new roller bearing in the tailhousing.
NOTE: For applications of 1200 h.p. and more - A 300M Billet OUTPUT SHAFT is STANDARD ON THE MEGA TORQ III
Polished output shaft |

|
R1: 4 PINION BILLET STEEL SPLINED FRONT PLANETARY
R2: LARGE ENCLOSED TORRINGTON BEARINGS
R3: HEAVY DUTY REINFORCED FRONT ANNULUS
R4: 4 PINION REAR PLANETARY
R5: HEAVY DUTY REINFORCED REAR ANNULUS
R6: ALUMINUM GOVERNOR REPLACEMENT
R7: LIGHTENED (ROLLERIZED) PARK GEAR
R8: BILLET STEEL ROLLERIZED DRIVETRAIN SUPPORT
R9: 16 ROLLER "ULTRA SPRAG" BOLT-IN SPRAG
R10: ROLLERIZED LOW/REV DRUM
PROVIDING THE BRUTE STRENGTH and RELIABILITY TO THE OUTPUT SECTION ARE:
The BILLET STEEL REAR SUPPORT provides the ultimate drivetrain stability and axial support possible
for the 727. Its' inherent strength effectively reduces the deflection and shaft misalignment that can
lead to accellerated wear on clutches, planetaries and bushings, resulting in greater reliability and reduced component
drag.
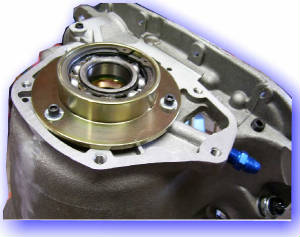
|
Mega Torq case with Billet Rear Support |
FEATURES OF THE ULTIMATE REAR SUPPORT |
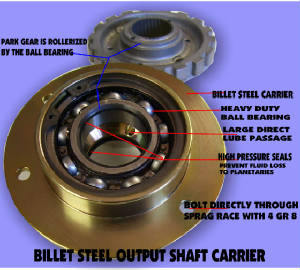
|
Unlike the modified stock aluminum supports with internal roller bearings providing support to the output shaft
and low/reverse drum used by many, this billet steel support utilizes heavy duty BALL BEARINGS that drastically
reduce resistance, provide dynamic load capacity (that eliminates shearing off the bearing support under extreme torque loads),
provides unrestricted lube flow to the output shaft and planetaries (needle bearings in the support create restriction in
lube flow generating heat) and provide stability for the rear drum preventing band drag and early wear.
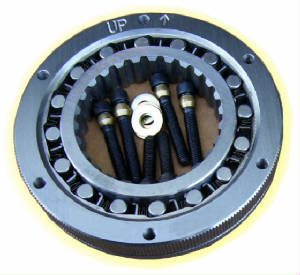
THE "ULTRA SPRAG" is the strongest, most reliable, roller clutch available.
For years the roller clutch (often referred to as the sprag) in the Torqueflite 727 was the weakest link and feared by
most for its' devistating impact on the transmission if it failed. The steep ramps and weak cast-in support in the rear
of the case would often fail in the event of driveline breakage or low gear burnouts.
Attempts were made to reduce this problem by drilling and threading the outer race to permit bolts through the case to
anchor it more securely, however under high torque applications the outer race would fail at the drilled bolt holes often
leading to high drum explosion.
The new design in roller clutch utililizes 16 rollers instead of the stock 12 providing a 30%
apply capacity increase. The ramp angles on the outer race are substancially reduced resulting in much less outward
shock load and a thicker stronger outer race preventing breakage of the outer race. The spring cage is dramatically
heavier than the stock unit to prevent the common rollover problem.
The roller race is secured to the case with 6 Grade 8 screws - 4 through the billet rear support and 2 through the case
for maximum capacity.
THE "DOUBLE WELDED" ANNULUS RING GEARS which prevents the event of component separation when
transferring the severe torque loads from the planetaries to the output shaft.
THE 4 GEAR ALUMINUM PLANETARY CARRIER which is machined to accept Torrington bearings that
eliminate drag, reduce heat and prevent metal fatigue created by friction stress.
THE 4 GEAR BILLET STEEL SPLINED FRONT PLANETARY. This setup eliminates the stripped
splines common with the stock aluminum splined planetary carriers. The billet Steel cover provides substancial
increase in load transfer capacity in 1st and 2nd gear application where the broached splines in the stock cast
carrier are extremely vulnerable to stripping under high torque. Note: The MegaTorq for street use or blower applications
uses a solid steel planetary carrier, while the race version uses the steel capped aluminum carrier for reduced inertia weight.
NOTE: OPTIONAL 8620 gear Steel, STRAIGHT CUT PLANETARY GEAR SETS in various
ratios, are also available
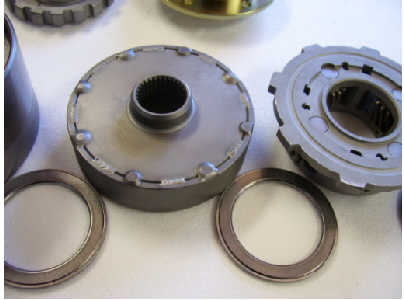
|
Welded annulus & planetary |
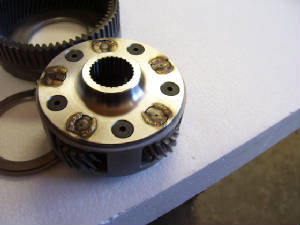
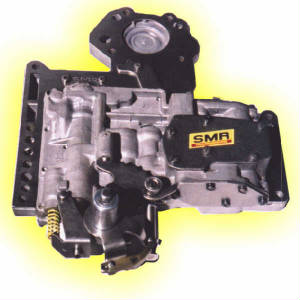
|
SMR COMPETITION ELIMINATOR VALVEBODY |
"REVERSE PATTERN" MANUAL VALVEBODY
Only the cleanest shifts (no shift overlap or lag) will provide the clutch apply necessary to handle the massive torque
loads for which the MegaTorq is designed. Converter apply pressures, lube and cooling circuits and anti-drainback functions
must also be precisely engineered into this valvebody.
Every MegaTorq (except for transbrake or certain street applications) is equipped with
our COMPETITION ELIMINATOR reverse manual valvebody to meet these strict requirements. For full details on
this valvebody click on picture>
OPTIONAL: Is the TRANSBRAKE Valvebody
(with operating features of the Competition Eliminator valvebody) with the ability to electonically lock the transmission
for instantaneous launches. and for certain Street Only Applications, a LOW BAND APPLY Valvebody.
SERVO PISTONS, BAND APPLY LEVER AND APPLY STRUT
The low/ reverse piston and return spring retainer are super strong, Billet
Aluminum components;
The 2nd gear apply piston retainer is Billet Aluminum with an internal seal
to maximize high clutch apply;
The 2nd gear apply strut is a heavy duty, billet, hardened steel component to prevent
flex and deliver the firmest band apply; and
The 2nd gear apply lever is a billet,hardened steel,4.2:1 ratio to increase the band
apply pressure for a quick, firm shift and to increase band clamping force.

CLUTCHES, STEELS, BANDS, SEALS, GASKETS and FILTER
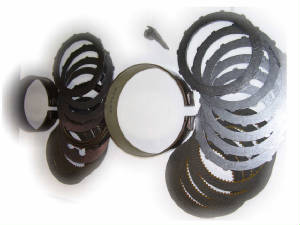
|
CLUTCHES, STEELS, PRESSURE PLATES and BANDS |
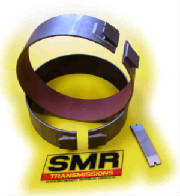
Only the best NORTH AMERICAN made frictions, bands, steels, seals, gaskets and filter are utilized in
an SMR Transmission. Utilizing an inferior material may be cheaper to purchase but it will drastically
reduce reliability and performance.
Every MEGA TORQ transmission utilizes a NEW COMPETITION CAST BAND (which is 10%
wider than the original 727 cast band), with a friction material selected to match the specific application in which
it will be used.
FRICTION MATERIAL (on clutch plates) is carefully selected to provide the ultimate performance
levels through the wide range of heat, pressure and speed without performance fade in the specific application for which
the transmission is constructed. Friction material selections of high energy Kevlar, Raybestos Stage 1 and gen2
Blue are utilized.
Superb quality STEELS designed with a specific surface texture to enhance the characteristics of the
friction material utilized and precision drive tabs to transfer torque to outer drive slots without distortion or accellerated
drum wear, are used.
Seals and gaskets are all American made components designed to withstand extended high pressure, high
temperature use without fatigue, advanced hardening or deterioration.
Sealing rings are a choice of selected chromemoly, teflon and precison metal components to assure longevity
and critical fluid transfer under extreme pressure.
ASSEMBLY and TESTING
Like all SMR Transmissions, every critical dimension and surface is carefully inspected and machined
to precise specification. All bearing surfaces, clearances, bores and end plays are BLUEPRINTED with
precision.
Every bearing and contact surface is assembled with and liberally coated with Moly-Slip ATS (a
Molybdenum LUBRICANT specifically formulated to remain in suspension in the fluid and adhere only to metal components without
reducing friction co-efficiency or adversely affecting seals) to prevent wear on startup and reduce the need to break-in
the unit.
Every aspect of the operation of the transmission is HIGH PRESSURE COMPRESSION TESTED to confirm precise
operation of all circuits. This method of testing assures peak performance of the finished product.
|